Our Services
Fabrication
WIEN Global is a leading provider of Fabrication Services and piping solutions. We have an extensive global experience for any tank construction in the industry, as well as offering turnkey solutions for atmospheric and pressure storage.
Our fabrication capabilities encompass piping and module prefabrication and assembly, as we design and build modular gas processing, gas recovery and synthesis gas production units.
We also design and build upstream as well as downstream process facilities for the oil and gas industry, such as refinery process units and petrochemical facilities, fossil and renewable electric generating plants for the power industry.
WIEN Global uses the latest fabrication technologies to enhance performance and reliability to meet project requirements. As a major provider of piping technology, we develop and use proprietary computer applications for design interface, material control, production scheduling and fabrication management.
We incorporate induction bending technology provided by Cojafex B.V., the world’s leading supplier of induction bending equipment for both pipe and structural shapes.
However Induction Bending is the preferred alternative to traditional fit and weld procedures due to its precision and accuracy, as well as the overall strength of the final product. We are able to bend a wide variety of materials including carbon steel, low and intermediate alloys (P11, P22, P5, P9, P91, P92 and others), stainless steel, duplex steel, all API X grades and nickel alloys.
Key features of our induction bending capabilities include the following:
- Nine induction bending machines:- Capable of bending up to 66 inches (1600mm) in diameter and 6 inches (150mm) in wall thickness and is also of capable of producing 1.5 diameter bends
- Multiple cold bending machines
- Structural shape bending equipment
Major advantages of induction bending are:
- Cost efficiency. Straight material is less costly than standard components (e.g. elbows) and bends can be produced faster than standard components can be welded.
- Elbows can often be replaced by larger radius bends, reducing friction, wear and required pump capacity.
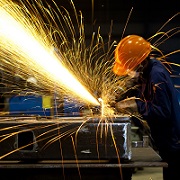
Induction bending reduces the number of welds in a system.
- No welds at the critical points thanks to the tangents
- Less non-destructive testing, saving cost
- Induction bends are stronger than elbows with uniform wall thickness
- Stock of elbows and standard bends can be greatly reduced
- Straight pipe is more readily available than elbows, reducing time to market
- Bends can be made from the same base material as the straight pipe
- Induction bending does not need bend dies or mandrels. A simple clamping/ inductor set covers a wide range of radii and wall thicknesses
- Induction bending is a clean process. No lubricants necessary